Obróbka elektroerozyjna (EDM) to proces produkcyjny oparty na kontrolowanej erozji materiałów przewodzących za pomocą elektrody. Obrabiarki elektroerozyjne są zwykle stosowane do uzyskiwania bardzo złożonych kształtów w ekstremalnie twardych metalach, takich jak węglik wolframu, tytan i utwardzone stopy stali narzędziowej.
Jak działa EDM?
Istnieją dwa rodzaje maszyn EDM: Elektrodrążarki wgłębne i Elektrodrążarki Drutowe. Działanie obu opiera się na tej samej zasadzie. Iskra elektryczna powstaje między przedmiotem obrabianym a naładowaną elektrodą, wykorzystując płyn dielektryczny jako medium do kontrolowania przepływu prądu. Maszyna sterowana CNC zbliża dwie elektrody na tyle blisko, aby zjonizować szczelinę i przegrzać powierzchnię przedmiotu obrabianego i elektrody.
Po osiągnięciu niezbędnej temperatury następuje rozładowanie i odparowanie materiału. Po usunięciu materiału generator wyłączy się na krótki czas, umożliwiając odparowanie odparowanych cząstek w płynie dielektrycznym. Proces ten powtarza się wielokrotnie przy częstotliwościach około 100 000 razy na sekundę podczas zgrubnych cykli obróbki.
W przypadku Elektrodrążenia drutowego rolę elektrody tnącej spełnia precyzyjnie wykonany drut mosiężny przeważnie o średnicy 0,25 mm. Drut jest prowadzony przez obrabiany przedmiot za pomocą precyzyjnych matryc diamentowych zarówno na górze, jak i na dole obrabianego przedmiotu.
Elektrodrążarki wgłębne zwykle wykorzystuje niestandardową elektrodę wykonaną z różnych materiałów, takich jak grafit (węgiel), miedź lub bardziej egzotyczne materiały, takie jak miedź wolfram.
Dlaczego EDM jest idealny do zastosowań w matrycach / formach?
Produkcja wysoce dopasowanych matryc i form wymaga wyjątkowej dokładności. Ponieważ mają wymagające punkty konstrukcyjne, takie jak ostre wewnętrzne rogi, wąskie szczeliny, głębokie żebra i inne skomplikowane kształty. Nie ma innego narzędzia, które mogłoby osiągnąć precyzyjną obróbkę wymaganą do produkcji elementów matryc i form bez dzielenia elementów na prostsze kształty.
Co więcej, zdolność EDM do osiągnięcia tak drobnego wykończenia powierzchni, integralności powierzchni i wysokiej precyzji minimalizuje lub eliminuje potrzebę polerowania i innych wtórnych procesów. Na koniec matryce są zwykle wykonane z bardzo twardych stopów stali, co powoduje konieczność obróbki zgrubnej i / lub wykończeniowej przed obróbką cieplną, co radykalnie zmniejsza dokładność detalu. Zwykle przekłada się to na niestandardową pracę ręczną, plamienie i montaż, co sprawia, że naprawa i konserwacja narzędzia jest czasochłonna i kosztowna.
Płyn dielektryczny
Elektrodrążarki wgłębne zwykle wykorzystują olej węglowodorowy do płynów dielektrycznych, w które zanurzony jest zarówno przedmiot obrabiany, jak i iskra. W przeciwieństwie do tego, elektroerozja drutowa zwykle wykorzystuje wodę dejonizowaną, w której zanurzony jest tylko obszar iskrzenia. Bez względu na to, czy jest to olej, czy woda, płyn dielektryczny stosowany w maszynach EDM spełnia trzy kluczowe funkcje:
- Kontrolowanie odstępu iskiernika między elektrodą a przedmiotem obrabianym
- Chłodzenie ogrzanego materiału z utworzeniem wiórów EDM
- Usuwanie wiórów EDM z obszaru iskrzenia
Chociaż są znacznie mniejsze niż te produkowane w procesach frezowania lub toczenia, EDM produkuje wióry. Te małe, wydrążone sferoidy składają się z materiału zarówno z elektrody, jak i przedmiotu obrabianego. Podobnie jak każdy wiór, należy je usunąć ze strefy cięcia, co osiąga się poprzez przepuszczenie płynu dielektrycznego przez iskrzącą szczelinę.
Gdy płyn dielektryczny rozpada się - w wyniku starzenia się lub zanieczyszczenia - wzrasta ryzyko niestabilnego rozładowania. Elektronika sterująca może w pewnym stopniu kompensować, ale jedynym realnym rozwiązaniem jest ciągłe pompowanie czystego płynu dielektrycznego przez strefę cięcia, aby go przepłukać. Im więcej cząstek przewodzących w płynie, tym trudniej jest utrzymać maszynie stabilne progi elektryczne wewnątrz iskiernika.
Ponieważ żywotność płynu dielektrycznego zależy od wielu czynników, takich jak jego rodzaj oraz wydajność i jakość filtrów płynu EDM, nie ma on ostatecznej daty ważności. Zasadniczo jednak, jeśli używasz płynu na bazie oleju i ma on ponad pięć lat, prawdopodobnie należy go wymienić. Możesz także wykonywać porównania wzroku i zapachu między używanymi i pierwotnymi płynami, ale najlepszym sposobem ustalenia, czy płyn dielektryczny wymaga wymiany, jest refraktometr.
Na przykład zawieszenie cząstek jest kluczową właściwością dla wydajności obróbki, ponieważ płyn musi być w stanie usunąć wióry EDM i inne cząstki odpadowe ze strefy cięcia. Jeśli jednak zawiesina cząstek jest zbyt wysoka, zanieczyszczenia te nie oddzielą się od płynu podczas filtracji.
Zalety EDM obejmują obróbkę:
- Złożone kształty, które w innym przypadku byłyby trudne do wytworzenia przy użyciu konwencjonalnych narzędzi skrawających.
- Niezwykle twardy materiał o bardzo małych tolerancjach.
- Bardzo małe elementy, w przypadku których konwencjonalne narzędzia tnące mogą uszkodzić element na skutek nadmiernego nacisku narzędzia tnącego.
- Nie ma bezpośredniego kontaktu między narzędziem a przedmiotem obrabianym. Dlatego delikatne sekcje i słabe materiały można obrabiać bez zauważalnych zniekształceń.
- Można uzyskać dobre wykończenie powierzchni; bardzo dobrą powierzchnię można uzyskać przez zbędne ścieżki wykończeniowe.
- Można uzyskać bardzo drobne otwory.
- Mogą być wytwarzane stożkowe otwory.
- Wewnętrzne kontury rur i pojemników oraz wewnętrzne narożniki do R .001 ”.
Wady EDM obejmują:
- Wolne tempo usuwania materiału.
- Dodatkowy czas i koszty związane z tworzeniem elektrod
- Odtwarzanie ostrych narożników przedmiotu jest trudne z powodu zużycia elektrody.
- Specyficzne zużycie energii jest bardzo wysokie.
- Pobór mocy jest wysoki.
- Podczas obróbki występuje zużycie elektrod, które wymagają regeneracji
- Materiały nieprzewodzące elektrycznie można obrabiać tylko przy specyficznym ustawieniu procesu.
Obróbka wielkogabarytowa EDM
W firmie Reg Form zajmujemy się obróbką dużych gabarytów. Obróbkę elektroerozyjną wykonujemy na maszynach ONA oraz Charmilles. Maksymalny gabaryt detalu to 2300x1500x1000mm. Waga detalu może osiągać nawet 15 ton. Elektrody niezbędne do procesu elektroerozji wykonujemy sami. Możliwe jest również wykorzystanie elektrod dostarczonych przez klienta.
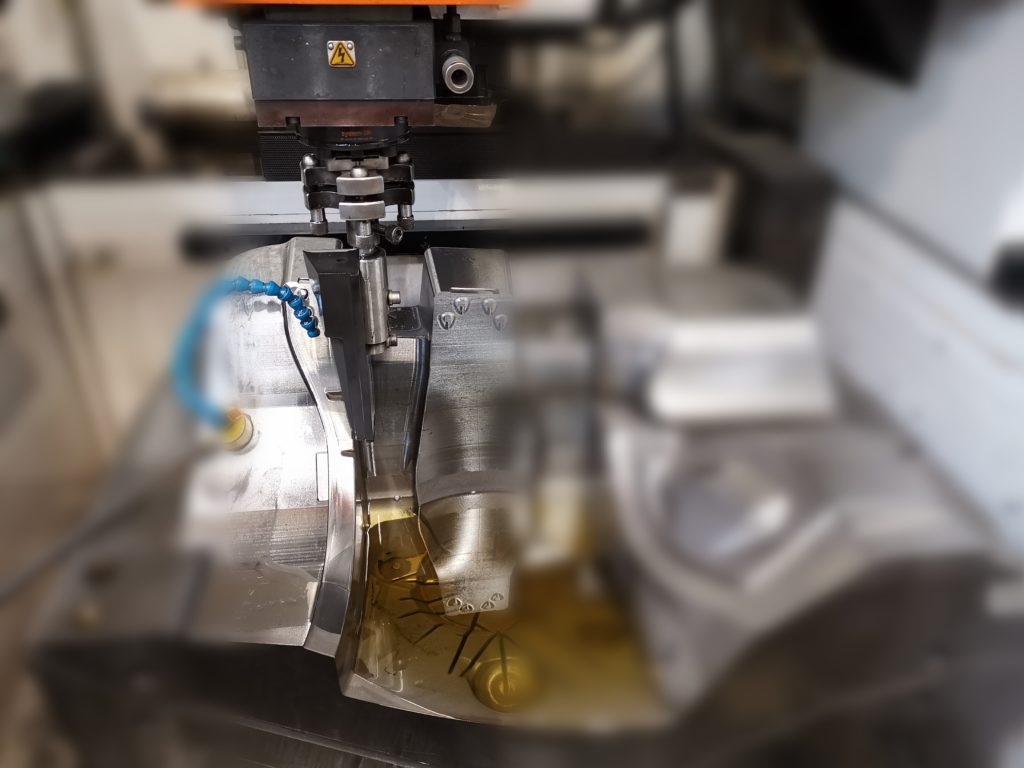